Why Safety Matters
Our company culture is based on safety, quality, cost-effectiveness, time management, and customer satisfaction. We understand that our employees are our greatest assets, and protecting them is important. That is why workplace safety and health are our core values here at Postler & Jaeckle.
We have a safety program that is a comprehensive evaluation of the dangers of some of our activities and how to avoid accidents that may occur. Our company conducts safety meetings to discuss incident trends, comparative safety performance, and new policies and procedures. The meetings also include training on new safety topics or Occupational Safety and Health Administration (OSHA) regulations.
We have a safety program that is a comprehensive evaluation of the dangers of some of our activities and how to avoid accidents that may occur. Our company conducts safety meetings to discuss incident trends, comparative safety performance, and new policies and procedures. The meetings also include training on new safety topics or Occupational Safety and Health Administration (OSHA) regulations.
Accident Prevention and Safety Policies
Safety Staff
Disciplinary Policy
Safety Recognition Program
Medcor
Incident reporting & investigation
Stretch and Flex Program
Safety Inspections
Toolbox Safety Meetings
Pre-Task Plans and Task Hazard Analysis
Job Hazard Analysis
Safety Committee
Site Specific Safety Plans
New Employee Safety Orientation
Safety Training
Awards
At Postler & Jaeckle, safety isn’t just a priority—it’s a core value. We take pride in maintaining the highest standards of workplace safety across all our projects. Our dedication to fostering a culture of safety has been recognized with numerous industry awards, reflecting our commitment to protecting our team members, clients, and the communities we serve.
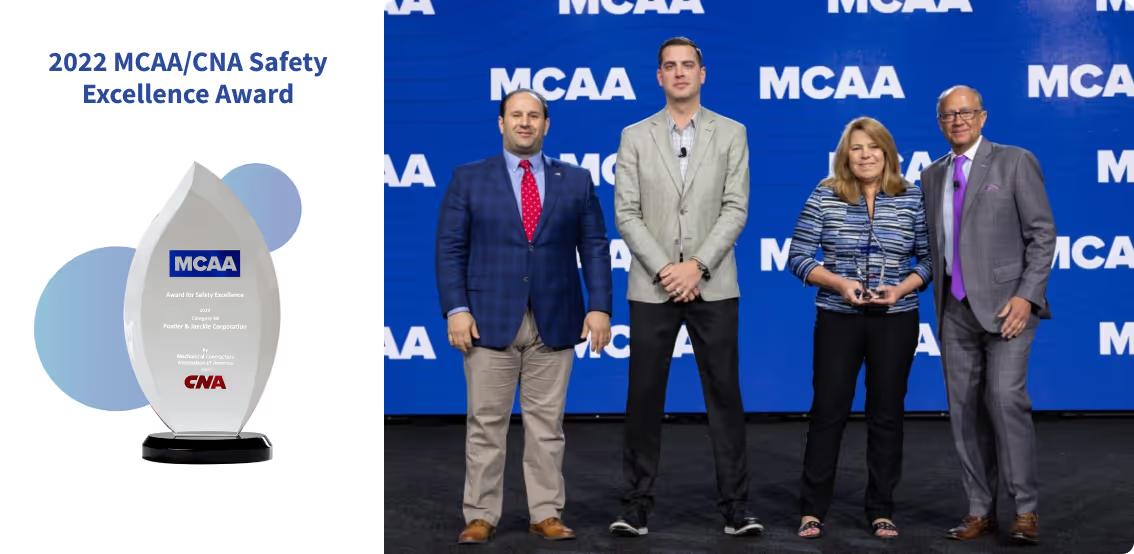
Our Safety Scorecard
Annual incident rates are a significant indicator of how safe our workers are in any company operation. It allows us to track our improvements in providing a safe workplace for our employees. The following charts show our incident rates for the past five years
OSHA Recordable (Total Cases)
Industry Average based on BLS NACIS Code for Plumbing, Heating, Air Conditioning
OSHA Lost Workday Cases
Industry Average based on BLS NACIS Code for Plumbing, Heating, Air Conditioning
Experience Modification Rate (EMR)
An Experience Modification Rate (EMR) below 1.0 is considered better than average.